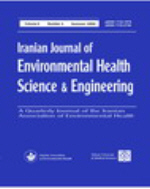
|
Iranian Journal of Environmental Health, Science and Engineering
Iranian Association of Environmental Health (IAEH)
ISSN: 1735-1979
Vol. 2, Num. 1, 2005, pp. 60-66
|
Iranian Journal of Environmental Health Science & Engineering,Vol. 2, No. 1, 2005, pp. 60-66
The Impacts of Macroergonomics on Environmental Protection and Human Performance in Power Plants
*A Azadeh 1, J Nouri 2, I Mohammad Fam, 1, 3
1Research Institute of Energy Management and planning and Dept. of Industrial Engineering, Faculty ofEngineering, University of Tehran, Tehran, Iran
2Dept. of Environmental Health Engineering, School of Public Health,Tehran University of Medical Sciences, Iran
3Dept. of Environmental Management, Graduate School of the Environment, Science and Research Campus,Islamic Azad University, Tehran, Iran
*Corresponding author: Tel: +98 21 4480 4162, Fax: +98 21 4480 4160, E-mail: aazadeh@ut.ac.ir
Code Number: se05010
ABSTRACT
Human and his performance is a vital factor in protection of asset including environmental properties. The objective of this study was to evaluate the impact of total system design factors (TSD) on human performance in a power plant. The TSD factors are defined as design factors, which have impact on overall performance of the power plants in context of total human engineering or macroergonomics. The systems being studied are the control rooms and maintenance departments of a 2000 MW thermal power plant. To achieve the above objective, the TSD factors were addressed and assessed through a detailed questionnaire. The relationships between TSD factors and human performance were then examined through non-parametric correlation analysis (Kramer’s Phi) and Kruskal-Wallis test of means. The results of this study show that the macroergonomic factors such as organizational and safety procedures, teamwork, self-organization, job design and information exchange, influence human performance in the power plant. The findings also suggest that the selected macroergonomic factors are correlated to human performance and must be considered, designed and tested concurrently with the engineering factors at the design phase of the system developmental cycle. Consequently, total system’s faults and organizational errors are reduced to an acceptable level and human performance is significantly increased. The main goal in such program is customer's satisfaction (Internal customers). However, more elaboration on the scientific tools for implementation of TDS factors in context of human performance is also under investigation. Keywords: Total system design, Environmental protection, Power plants, Human performance, Ergonomic, Macroergonomics
INTRODUCTION
The utilization of modern technology has de-veloped industries that are more complex in the last decade. In the recent years, technological development has created major crisis accidents such this modern technology has been extensively questioned by scientists. One of the se-vere impacts of this crisis is the environmental property. For example, Chernobyl nuclear acci-dent in 1986 has cost between 7000 to 10,000 lives (Shivastava, 1988). It cost about 26 bil-lions for housing of 200,000 people who were affected by radiation. In addition, the total cost of this accident was estimated around b$ 400,000,000 and minimum time to eliminate the impact of radiation pollutant region was es-Macroergonomics is an integrated develop-timated around 200 years (Meshkati, 2002). mental process, which is based on a series of In complex systems such as process plants, pet-well-defined phases. Macroergonomics requires rochemical and chemical industries, human op-equal consideration to all major components of erator plays an important and critical role. The the system such as human, hardware, software impact of human error can be sever and lead to and organizational structures. Indeed, it is quite catastrophic accidents in such systems. Analy-important to pay serious attention to human and sis of these environmental disasters have shown organizational aspects of the macroergonomics in Table 1 (Azdeh et al., 2000). process from early design phase.
Table 1: The causes of some major environmental disasters (Azadeh et al., 2000)
Causes of accident/ Failure |
Name of accident | Managerial error | Human factor | Inadequate interface design | Safety issues | Inadequate system design |
---|
Chernobyl nuclear power plant | * | * | * | * | * | accident (1986) | | | | | | TMI nuclear power plant accident | * | * | * | * | * | (1979) | | | | | | Bhopal chemical processing plant | * | * | * | * | * | accident (1983) | | | | | | Aloha airlines accident (1988) | | * | | | * | U.S. telephone network accident in | | | * | | * | Chicago suburb(1988) | | | | | | Thirty major accidents in chemical | * | * | | | | plants (1985-1989) | | | | | | NASA’s space shuttle explosion | | | | | * | (1986) | * | | | | | Proctor& Camble Tylenol (1982) | * | * | | | * | U.S. public phone network outage | * | * | * | | * | (1991) | | | | | | British Piper Alpha explosion | * | | | | * | (1988) | | | | | |
Total system design factors in context of human performance are referred to as socio-technical factors in context of system design. It should be noted that the engineering design process is of-ten perceived as mainly technical activity, yet within engineering design organization it really only coheres as a social activity. This paper in-troduces the socio-technical factors as essential and vital part of the design process and preven-tion of accidents (and environmental protec-tion) in power plants and because they are re-lated to overall management and organization structures, referred to as TSD factors in context of human performance (Clegg, 2000; Lloyd, 2000; Sutcliffe, 2000).
TSD factors in context of human performance define the macroergonomics features of the system design and human performance engi-neering, whereas, the conventional system de-sign factors in context of human performance define the ergonomics features of the system design and human performance engineering.
Ergonomy attempts to optimize the interaction between human operator and machine. It con-siders those factors of machine, design and work posture that affect the user interface and working conditions related to the job or task deign. In a macroergonomics study, the ergo-nomics factors are considered in parallel to or-ganizational and managerial aspects of working conditions in context of a total system design. Moreover, it attempts to create equilibrium be-tween, organization, operators and machines. It focuses on total "people-technology" systems and is concerned with the impacts of techno-logical systems on organizational, managerial and personnel subsystems (Azadeh and Hooshiar, 1998; Hendrick, 1995).
MATERIALS AND METHODS
Macroergonomic factors in context of human performance are defined as factors influencing total system's performance, such as rules and procedures and information exchange between personnel/ departments. To measure the im-pacts of macroergonomic factors on human per-formance, a quesionnair was designed and handed out to all control room and maintenance operators. It was designed based on total system design (TSD) aspects of human performance in power plants. Moreover, key macroergonomics factors were included to evaluate human per-formance. The selected TSD factors are related to procedures, work assessment, teamwork, self -organization, information exchange and com-munication. They were inputted to the ques-tionnaire and their statistical relationships to the human performance were examined through two non-parametric statistical (namely,Cramer's Phi and Kruskasl-Wallis) approach. The se-lected TSD factors in context of human per-formance were tested in the following format:
- Degree of familiarity with rules and proce-dures
- Supervisors' monitoring and assessment at work
- Reward for teamwork by supervisors -Ease of contact with supervisors
- Problems with co-workers due to inter-organ-izational relationship
- Quality of perceived information from supervi-sors
- Quality of perceived information from co-workers
- Usefulness of informal information exchange
- Freedom for self-organized and individual decision-making
As mentioned, a set of non-parametric test of hypothesis was conducted to foresee if human performance was independent of the selected TSD factors. Furthermore, job pressures were selected as the factor representing human per-formance since it was identified as one of the most important human shaping factors (Wiens, 1996). The sources of job pressures in the power plants were classified as 1) workload, 2) stress and 3) time considerations (Bahr, 1997). Because workload was identified as the most influential source of job pressures, it was se-lected as the measure of human performance in this study. It was tested whether job pressures due to workload is influenced by the TSD fac-tors. In addition, the difference between mean ratings of operators with respect to selected TSD factors were examined through Kruskal-Wallis test. All operators and supervisors of control rooms and maintenance departments participated in this study. Furthermore the study was based on entire populations in both de-partment rather than sampling.
RESULTS
The Cramer's Phi statistic tests the null hy-pothesis (H0) of no correlation between the two variables against alternative hypothesis (H1) of correlation between the two variables (Hinton, 1996). The results of the non-parametric Cramer's Phi correlation between human per-formance (job pressures) and the nine TSD factors are presented in Table 2. As shown, there is strong evidence that the teamwork. Operators who are rewarded for nine-macroergonomic factors are correlated teamwork report lower level of job pressures with the job pressures at work. Furthermore, the and consequently produce higher performance. job pressures at work are influenced by famili-The freedom for self-organization is positively arity with organizational rules and procedures correlated with human performance. In sum-and information flows between co-workers as mary, these findings suggest the positive im-well as co-workers and supervisors. In addition, pacts of macroergonomic factors on human per-job pressures are positively correlated with formance. Table 2: Test of correlation between human performances (job pressures) and the selected TSD factors TSD factor | Cramer's Phi | P-value (α) |
---|
1. Degree of familiarity with rules and procedures | 0.67 | 0.00000 |
---|
2. Supervisors' monitoring and assessment at work | 0.40 | 0.00900 |
---|
3. Reward for teamwork by supervisors | 0.55 | 0.00002 |
---|
4. Ease of contact with supervisors | 0.50 | 0.00002 |
---|
5. Problems with co-workers due to inter-organizational issues | 0.61 | 0.00000 |
---|
6. Suitability of perceived information from supervisors | 0.56 | 0.00000 |
---|
7. Suitability of perceived information from co-workers | 0.45 | 0.00008 |
---|
8. Usefulness of informal information exchange | 0.43 | .00017 |
---|
9. Freedom for self-organized and individual decision-making | 0.50 | .00002 |
---|
To further our investigation, by using Kruskasl-Wallis test, series of comparative studies were performed between various groups of operators in the next section. It was examined if macroer-gonomic factors influence the human perform-ance in particular and the system in general. To achieve this objective, two groups of operators are examined on the selected response vari-ables. The selected response variables were the quality of information perceived from supervi-sors and co-workers and job pressures (human performance). The summary of the results are listed below:
Operators who received no on-the-job training report higher level of job pressures.
The quality of perceived information from su-pervisors is higher for the operators who re-ceive on-the-job training.
Operators who do not receive safety training report higher level of job pressure. This with the above findings requires consideration of on-the-job and safety training as two TSD features at the design phase. For the power plant of this study in particular and other power plants with similar deficiencies in general, it requires the re-designing of the training system, such that it is spread to all sensitive areas of the plant.
Operators who are capable of locating emer-gencies report higher quality of perceived in-formation from co-workers. Operators who do not have any problem with organizational procedures report lower level of job pressures.
Operators who violate safety procedures due to job pressures report higher level of job pres-sures during routine situations.
Operators who do not have any problem with organizational procedures report higher quality of perceived information from supervisors.
Operators who do not have any problem using organizational procedures report higher quality of perceived information from co-workers.
Operators who do not violate safety procedures due to job pressures report higher quality of perceived information from co-workers. This and the last five findings highlight the impor-tance of organizational and safety procedures as two vital elements of TSD in context of human performance. The standardization of organiza-tional and safety procedures may be a good start for re-design of the existing procedural system. This may be achieved by implementa-tion of ISO 9000 and 14000 and OHSAS 18000 which are international standards for docu-mentation of organizational, environmental and hygiene and safety procedures, respectively.
Operators who have freedom to make decisions without continuous contact with others report higher quality of perceived information from supervisors. Operators who cannot easily communicate with supervisors report higher level of job pressures.
Operators who can easily communicate with supervisors report higher quality of perceived information from supervisors.
Operators who do not have problem with co-workers due to inter-organizational issues re-port higher quality of perceived information from supervisors.
Operators who have problems with co-workers due to inter-organizational issues report higher level of job pressures.
Operators who are rewarded for teamwork re-port higher quality of perceived information from co-workers.
Operators who are rewarded for teamwork re-port lower level of job pressures. Clearly, team-work is a key ingredient of the TSD in context of human performance (also see the last six bullets). Teamwork or groupthink must be spread from top to bottom in order to become most effective. This may be achieved through the deployment of re-engineering concept for the existing power plants (including the case of our study) and information exchange technol-ogy in context of information technology.
Operators who believed that there could be a better job design reported higher level of job pressures. This is an important finding, which reveal the current system of job design is par-tially rather than totally optimized. This is due to lack of considerations of the TSD factors of when the current system of job design was de-signed and implemented. This means the exist-ing system of job design must be re-engineered. The significant levels of the tests (α) on the quality of perceived information from supervi-sors (macroergonomic factors) and human per-formance (job pressures) are summarized in Tables 3 and 4, respectively. The last column in Tables 3 and 4 define the relative advantage of group 1 over group 2 in relation to the quality of information perceived from supervisors and co-workers, respectively. Furthermore, the rela-tive statistical advantage of group 1 over group 2 is tabulated by the percent increase in quality of information perceived from supervisors and co-workers, respectively. The last column in Table 3 defines the relative advantage of group 1 over group 2 in relation to the job pressures. The significant difference between the groups of operators who are utilizing the macroergo-nomic factors and the groups who are not with respect to the response variables reveal that macroergonomic factors extensively influence the human performance in particular and the system in general.
Table 3: The significant level of test of comparison on the quality of information perceived from supervisors Table 4: The significant level of test of comparison on the job pressures (human performance)
|
Difference in mean ranking |
|
|
Parameters | Group* 1 Group 2 | P-Value (α) | Relative Advantage (%) |
---|
On-the-job training | 65 | 21 | 0.0856 | 30 |
---|
Problem with organizational procedures | 46 | 13 | 0.0030 | 60 |
---|
Rewarded for teamwork | 38 | 29 | 0.0041 | 40 |
---|
Individual decision-making capability | 41 | 21 | 0.0454 | 30 |
---|
Communicate with supervisors | 43 | 19 | 0.0164 | 40 |
---|
Problem with co-workers due to inter-Organizational issues | 8 | 54 | 0.0123 | 32 |
---|
Group*: Two compared groups, for example with and without “on-the-job training”
Table 4: The significant level of test of comparison on the job pressures (human performance)
|
Difference in mean ranking |
|
|
Parameters |
Group 1 Group 2 | P-Value (α) | Relative Advantage (%) |
Safety training |
57 |
8 |
0.0924 |
30 |
Problems with organizational procedures |
62 |
16 |
0.0100 |
40 |
Rewarded for teamwork | 48 | 19 | 0.0009 | 50 |
---|
Violate safety procedures | 35 | 29 | 0.0030 | 70 |
---|
Communicate with supervisors | 34 | 11 | 0.0054 | 45 |
---|
Problems with co-workers due to inter-organizational issues | 54 | 8 | 0.0073 | 58 |
---|
Believing a better job design is required | 57 | 7 | 0.0139 | 45 |
---|
The Kruskal-Wallis test of comparison between the two groups verifies and validates the previ-ous results obtained from the test of correlation between TSD factors and job pressures. It can be concluded that TSD factors significantly in-fluence human performance and therefore they must be considered and designed concurrently with other conventional hardware and software factors in order to optimize human performance in particular and the system in general.
DISCUSSION
The conventional design approach in power plants considers the engineering design pa-rameters and ergonomics factors (in some cases). However, TSD approach of this study in context of human performance considers the engineering design parameters and macroergo-nomics factors. The impacts of macroergo-nomic factors on human performance and envi-ronmental protection aspects are shown in this paper. This is shown through design and evaluation of a detailed survey containing in-formation about macroergonomic factors and human performance. It has been shown that a macroergonomic approach in context of human performance is much more efficient than a con-ventional design approach. This is shown through introduction of the macroergonomic model, applying the model in a power plant and showing its advantage through statistical analysis.
Non-parametric statistical analyses are used to show positive correlation between human per-formance and macroergonomic factors and to highlight the impact of macroergonomic factors on human performance. Furthermore, it is noted that by designing and implementing a macroer-gonomic approach, the system and its human element are totally rather than locally optimized in context of human performance.
It should be noted that the conventional design approach in context of human factors is only capable of identifying local or stationary human performance issues. This study shows that the employment of a macroergonomic approach is superior to conventional design approach. The findings of this study have several design implications. Rules and procedures, information exchange between personnel (operators and su-pervisors) teamwork and self-organization may be designed and accommodated through stan-dardization of the documentation process and automated tracking systems. This may be achieved through:
Implementation of ISO 9000 series of standards to promote standardization of documentation (rules, procedures, guidelines and communica-tions) process.
Implementation of ISO 14000 to develop stan-dardization of documentation process for envi-ronmental management systems.
Implementation of OHSAS 18000 to develop standardization of documentation process for safety management and occupational hygiene systems.
Design and implementation of automated in-formation exchange in context of information technology. This would facilitate and enhances the existing information structure.
Design and implementation of the re-engineer-ing concept may enhance organizational rela-tionships and surveillance. Re-engineering is the collection of activities and mechanisms re-quired changing from hierarchical to horizontal, flat and cross-functional structures based on teamwork within an organization.
REFERENCES
- Azadeh M A, Hooshiar M (1998). An integrated macro ergonomics model to enhance the productivity and working conditions of an assembly shop. CSME Forum SCGM, Ryerson University of Technology, Toronto, Canada.
- Azadeh M A, Keramati A, Jamshidnezhad B (2000). Enhancing the availability and reli-ability of power plants through macroergo-nomics approach. Energy: Proceedings of the 8th International Energy Forum, Las Vegas, July 23-8.
- Bahr N J (1997). System Safety Engineering and Risk Assessment: A practical ap-proach. London: Taylor & Francis.
- Clegg C W (2000). Sociotechnical principles for system design. Applied Ergonomics: 31(5): 463-477.
- Hendrick H W (1995). Harmonizing re-engi-neering for true organizational effective-ness: A macroergonomics approach. Pro-
- ceedings of the Human Factors and Ergo-nomics Society, 2: 761-65.
- Hinton P R (1996). Statistics Explained. New York: Rout ledge.
- Lloyd P (2000). Storytelling and development of discourse in the engineering design process. Design Studies, 21(4): 357-73.
- Meshkati N (2002). Ergonomic:, now and to-morrow. National Conference on industry and production. Iran.
- Sutcliffe A G (2000). Requirement analysis for socio-technical system design. Information Systems, 25(3): 213-33.
- Wiens J A, Parker K R (1996). Analyzing the Effects of Accidental Environmental Im-pacts: Approaches and Assumptions. Zecol Appl, 5 (4):1069-83.
© Tehran University of Medical Sciences Publications 2005
|